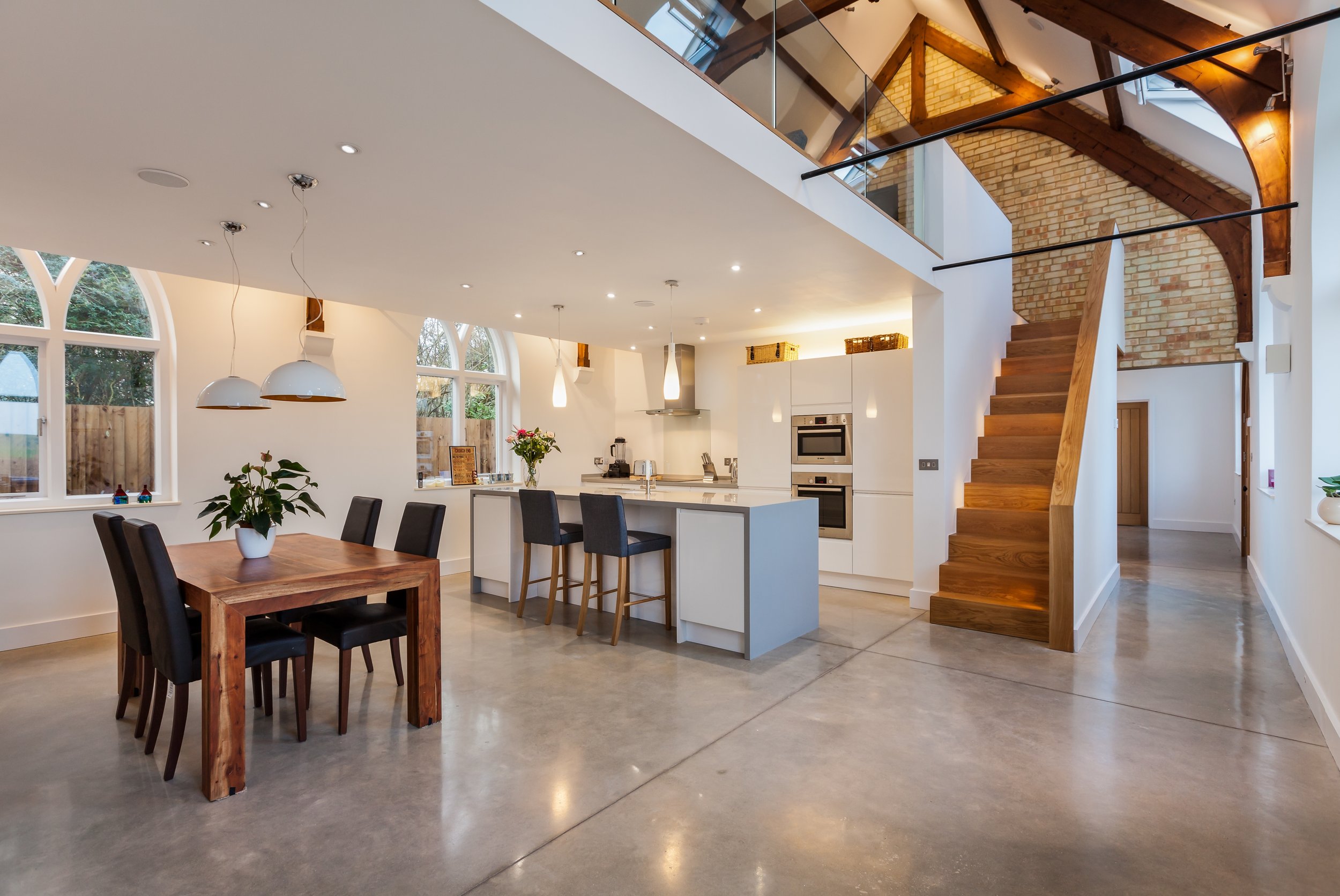
Mechanically Polished Concrete iS the process of using diamond abrasive tooling, grouts (if needed), densifiers, sealers and burnishing to grind, hone and polish concrete. This flooring system can be achieved with older, new and/or coated concrete. These diamond abrasive tools mechanically place micro scratches in the concrete and as we move to higher grit resins, refining the floor, these micro cuts become smaller and smaller, honing the concrete surface. Each individual project includes the process of densification which aids in trapping in dust and strengthen the concrete to its maximum hardness. In many cases, a grouting coat is required to fill the peaks of the scratches and micro pinholes. This process will reduce dirt and debris from getting trapped between these scratches and pinholes, and makes it much easier to maintain a clean floor. In summary, the objective of concrete polishing is to refine the floor to its desired aggregate exposure and reflective sheen, while creating a non porous, extremely durable surface. Due to the absence of a topical coating, there is little maintenance or need for floor re-coatings as we see with many other floor systems. This in turn makes true mechanically polished concrete a better long term investment and bang for your buck.
BENEFITS
-
Though polished concrete presents as a high-end luxury flooring system, it is actually more affordable than most other flooring options. The look of polished concrete provides an appealing, complete look without the need of other floor coverings such as tiles, vinyl or laminate. Because no floor covering materials are required, this enables concrete polishing to be a much more cost-effective flooring solution. Additionally, there is never a need to worry about polished concrete chipping, pealing, bubbling, or wearing off.
-
Unlike most decorative flooring options, polished concrete is relatively easy to maintain. There is no need to strip or wax the surface; simply keeping the floor dust & debris free & maintaining the burnish schedule designed for the space is the extent of maintenance required to keep its shine and last for decades.
-
In time, concrete will age, begin to crack & other problems can arise. Mechanically grinding a concrete floor removes the top surface of the concrete, while polishing then strengthens the floor, greatly increasing its impact & abrasion resistance. The floors will not be as vulnerable to deterioration as other materials, and in turn do not stain or chip nor need replacing. Polished concrete floors are extremely durable & if properly installed & maintained, can last over a century, even with excessive wear & tear.
-
Polished concrete is sealed, smooth & nonporous. This stops the floor from trapping any mold, mildew, dust mites, bacteria, allergens or moisture like other floors do. This makes it the most ideal choice for spaces where air purity is a must.
-
Polished concrete does not require coatings, adhesives or hazardous chemical coatings for maintenance or installation, making them a more eco-friendly flooring option.
-
Concrete polishing comes in a wide array of options to choose from. You can customize the level of shine, the colours, the aggregates & the patterns.
-
The high-gloss finish of polished concrete floors provide a very reflective surface that brings more light to spaces without the need for as many artificial light sources. This is preferable in offices, restaurants, hospitals & other public facilities with the desire to project a well illuminated, professional environment, all while reducing the cost of lighting.
F I N I S H O P T I O N S
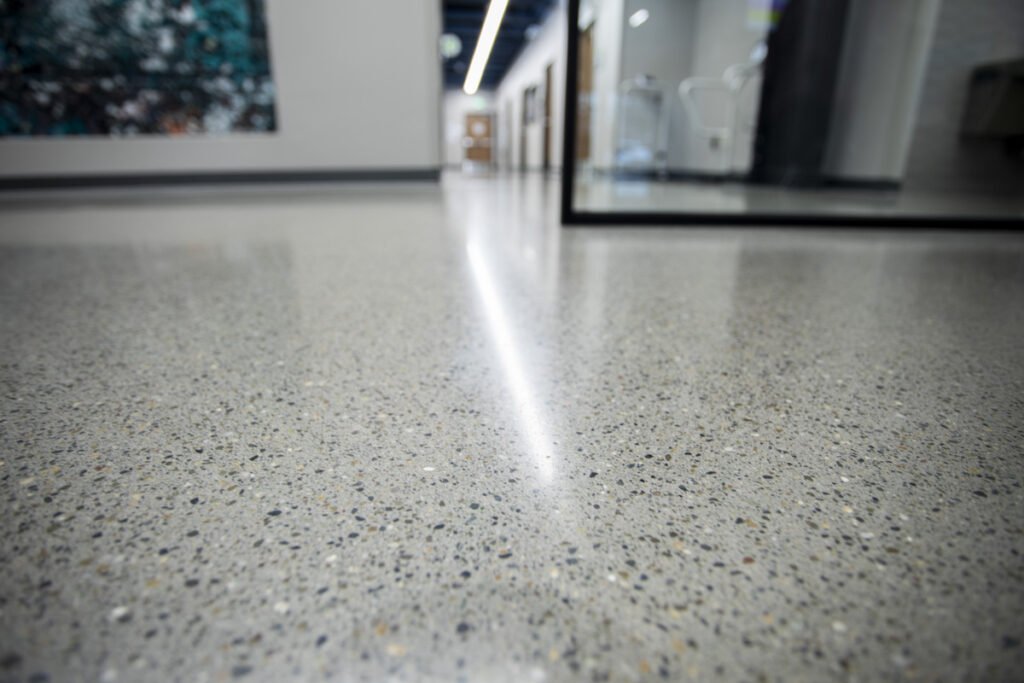